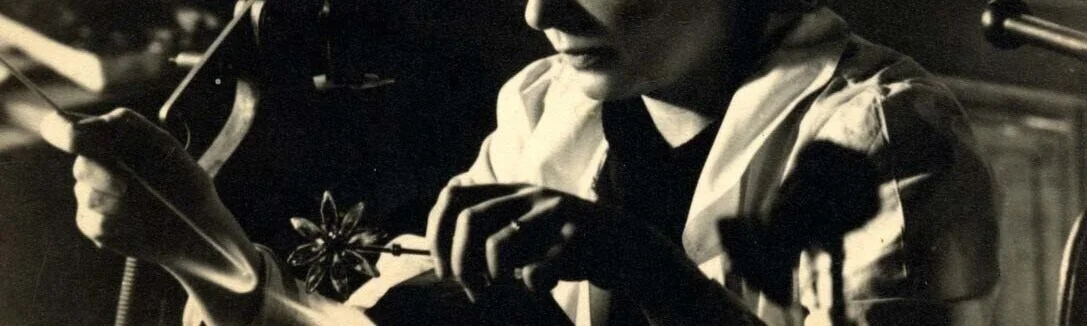
The know-how
Augustine's jewelry is the result of the founder's passion and expertise, inherited from the family know-how:
the art of molten glass.
A recognized craft.
The Maison Augustine holds the Entreprise du Patrimoine Vivant (EPV) label. A recognition from the French state, alongside the famous arts and crafts - such as Goosens, Lemarié or Lesage - to distinguish and preserve excellent craftsmanship and industrial know-how.
Hand-made by craftsmen in our Parisian workshop, they are born after long hours of meticulous work.
Each creation is a unique piece.
THE GOLDSMITH'S
The metal work carried out by the Maison Augustine's jewellers is close to finejewellery. The craftsman works the copper, which he shapes, stretches, sculpts with the help of multiple tools, and then uses his blowtorch to weld all the elements one by one in order to assemble them to give birth to the piece of jewellery.
THE GLASS MELT
Once the jewel has been assembled, it then goes to the "glass melting", a rare specific enamelling, perfectly mastered by the Maison Augustine's craftsmen, who position the glass above the flame at 800° of the blowtorch to soften it. The molten glass is then delicately placed in the cavity prepared by the jeweller. This technique requires great dexterity and years of training to accurately dose the amount of glass required for the balance of the piece of jewellery.
THE ASSEMBLY PROCESS
The finishing of the jewel consists of the assembly of the petals, of the rhinestones, and the closing systems. The final stage of the surface treatment is gilding: the piece is dipped in a bath of 24-carat fine gold, which gives it the final desired finish.
